In March 2025, a new 25% tariff on imported vehicles and parts forced companies like Stellantis to stop production at plants in Canada and Mexico and to lay off over 900 U.S. workers, marking a rapid shift in manufacturing setups.
Major U.S. automaker shares, including those of General Motors and Ford, declined as investors reacted to rising production costs and supply chain adjustments caused by the tariffs.
The adjustments and layoffs have generated a pool of experienced technicians, engineers, and production specialists that can be redirected to support increased domestic production.
Recruiters are now essential in reassessing job roles and matching the surplus talent to new positions within U.S. production facilities, while coordinating training programs and internal reassignments to fill critical operational gaps.
From Policy to Paycheck
In late March 2025, President Trump’s tariff announcements sent immediate shockwaves throughout the automotive industry and beyond. With new 25% tariffs imposed on imported vehicles and automotive parts—effective from early April—major manufacturers have been forced to quickly adjust their operations.
For example, Stellantis reported that it had temporarily laid off more than 900 U.S. workers across five of its facilities while pausing production at plants in both Canada and Mexico. These significant operational moves, documented by Reuters and Business Insider in March and early April 2025, are a stark reminder that government policy changes can rapidly influence production lines and employment figures across multiple sectors.
This unfolding scenario is not limited to the automotive industry alone. The domino effect of these tariffs is evident in the stock market fluctuations, with U.S. automaker shares—such as those of General Motors and Ford—experiencing noticeable declines as investors digest the immediate cost increases and production reallocation challenges.
Analysts are warning that the heightened tariff rates and subsequent production changes could raise overall production costs, potentially translating into higher consumer prices while complicating supply chains that have relied on decades of near-tariff-free operations.
This post-tariff reality calls for a proactive strategy—one that matches the speed of policy shifts with tactical talent realignment to keep businesses competitive even when faced with adverse external economic pressures.
Tariffs Trigger Talent Surplus: A Pattern Worth Watching
Recent policy changes announced by President Trump in March 2025 have altered automotive production and employment strategies across North America. As companies adjust manufacturing plans under the weight of a 25% tariff on imported vehicles and parts, production cuts and temporary layoffs have become common.
Automakers such as General Motors and Ford also experienced operational shifts as they concentrated production domestically to offset tariff-induced costs.
This shift in operations has led to a surplus of experienced workers in the automotive sector. Rather than being viewed only as job losses, these layoffs represent a redistribution of talent that can be redirected to sectors currently experiencing demand. Industry executives have pointed out that while some companies are forced to cut costs, the delayed production in foreign facilities has freed up a pool of skilled workers.
These professionals include technicians, engineers, and production specialists who now possess hands-on experience with advanced automotive manufacturing techniques—a resource that recruiters and business leaders can tap to address emerging needs in clean-energy transport, advanced manufacturing, and even technology-focused roles within traditional industries.
Market analysts have noted that tariffs, by raising the cost per vehicle by several thousand dollars, pressurize manufacturers to rethink their production strategies. As companies adjust by shifting capacity from international facilities to U.S.-based operations, the resultant talent surplus offers an opportunity to realign the workforce to areas where domestic production is rising. This situation creates a fertile context for reassigning skills into new roles and adapting workforce planning strategies, as automotive talent becomes available for redeployment into second chance hiring programs and training initiatives aimed at supporting expanded domestic production.
Recruiters’ Role in Workforce Realignment
The shifts in manufacturing due to the new tariffs have led to a surplus of skilled workers. Rather than a complete loss, the layoffs represent an opportunity to reposition talent. In March and April 2025, companies that previously relied on overseas facilities have reduced their workforces as production moves from foreign plants to domestic sites. This change creates a talent pool of professionals—including technicians, engineers, and production experts—with valuable experience in high-quality automotive manufacturing.
Recruiters are taking center stage by acting as architects of second chances. Their role now extends to matching these skilled workers with new positions that arise from shifts in production and operations. Recent insights from industry experts indicate that several U.S. automotive manufacturers have been forced to realign their workforce due to the tariff-driven production changes.
This shift has been decades in the making. Bersin recalls how Jack Welch’s forced ranking at GE sparked an era of aggressive downsizing, followed by the rise of agile teams, two-pizza teams, and self-managed structures at companies like Amazon and Facebook. Today, leaner, flatter organizations are becoming the norm, with companies like Meta, Goldman Sachs, and Amazon eliminating redundant roles and restructuring teams to align with new business realities.
However, as Bersin warns, workforce efficiency is not just about cutting jobs—it’s about restructuring wisely. The risk isn’t just overstaffing but also losing critical talent that could drive future growth.
Recruiters, therefore, become crucial players in this equation. By focusing on strategic hiring, reskilling programs, and internal mobility, recruiters can help businesses restructure with foresight, ensuring they retain and attract the right talent for long-term success. In a market flooded with displaced professionals, smart recruiters have a choice: react to the global layoffs as a hiring rush or proactively help companies build sustainable, future-ready teams. The latter is where true value lies.
Key points on the recruiters’ role in workforce realignment include:
Skill Redistribution:
- Layoffs from tariff-related production shifts are now creating a pool of experienced workers.
- These workers bring specialized expertise from their time in international facilities, which is valuable for expanded domestic manufacturing.
Matchmaking and Reassignment:
- Recruiters are actively matching available skills with emerging jobs in sectors where companies are increasing their domestic output.
- They are working closely with HR teams to redesign job roles and training programs that fit the new operating model within the automotive industry.
Supporting Internal Adjustments:
- Companies have begun initiating in-house training programs to help laid off workers acquire new skills suited to domestic production challenges.
- External partnerships with technical institutes are being formed to help workers adapt their skills to meet changing industry demands.
Second-Chance Hiring Strategy:
- Recruitment efforts now focus on providing workers a chance to continue using their hard-earned skills in roles that contribute to the reconfigured production processes.
- This approach not only supports workers in retaining their employment but also helps companies fill critical positions quickly.
What Smart Recruiters Should Be Asking Right Now?
As the tariff measures take effect and force companies to shift production and restructure operations, recruiters must ask pointed questions that drive new hiring strategies. Recent developments in March and April 2025 reveal that manufacturing adjustments have triggered a need to reexamine internal roles and capabilities.
In this context, recruiters should ask the following questions:
What work is currently unattended because it does not clearly match an existing job description?
Companies are finding that traditional job roles do not cover emerging tasks linked with domestic production. For example, the reallocation of production from foreign plants to U.S. facilities has introduced new operational demands such as increased quality and safety monitoring, changes in assembly processes, and the management of alternate supply chain protocols. Recruiters must pinpoint duties that have emerged but remain unassigned.
Which skills are being lost at a faster pace than they are being replaced?
With manufacturing shifts causing layoffs—like the 900 temporary positions cut at Stellantis—experienced employees with technical know-how are available in the market. It is critical to assess if key skills, particularly those in advanced automotive manufacturing and quality control, are disappearing faster than new talent can fill these roles. Recruiters need to identify skill gaps and determine which specialized abilities now require immediate attention.
Which laid-off workers could serve in future leadership positions?
Not every reduction in force is a loss of potential. Many of the workers who lost their jobs during these operational adjustments have valuable experience and institutional knowledge. Identifying those individuals who have demonstrated strong problem-solving skills, technical expertise, and a capacity for mentoring can help companies prepare for long-term workforce stability. This approach will support internal succession planning as companies reconfigure their teams to meet the demands of increased domestic production.
If tariffs force shifts in the supply chain, which new roles will emerge – and where?
The movement of automotive production back to U.S. facilities and the related changes in the supply chain generate demand for positions that did not previously exist. Recruiters should inquire:
- Will there be a need for additional roles in logistics and regulatory compliance?
- Are there new support functions required to integrate cross-border supply chain data with domestic operations?
- Which locations might see a rise in job opportunities as companies establish new production sites or expand existing operations?
Action Plan: Turning Tariff Turmoil into Talent Strategy
In response to the recent tariff-induced production shifts and layoffs in March and April 2025, companies in the automotive sector are reworking their workforce strategies. This presents recruiters and HR leaders with specific steps to adjust their hiring and training practices immediately.
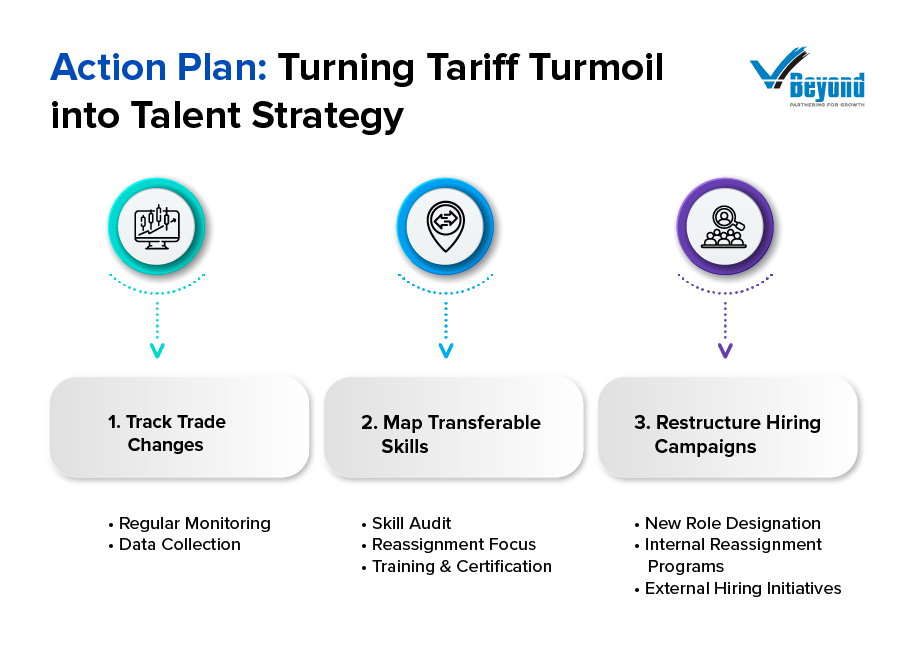
Below is a set of targeted actions that recruiters can implement now to mitigate the impact of these policy changes and reassign available talent to new roles arising from internal production shifts.
1. Track Trade Changes to Identify Talent Needs
Recruiters must keep close watch on trade policy updates and manufacturing decisions that have been announced by automakers. Monitoring these operational shifts provides a clear indication of emerging hiring priorities. HR teams should do the following:
Regular Monitoring:
- Review updates and reports from reliable news sources and industry analysts to capture the latest production adjustments.
- Stay informed on policy moves and tariff developments announced from March to April 2025.
Data Collection:
- Coordinate with operations to receive real-time feedback on production shifts and corresponding labor reductions.
- Access reports detailing the extent of layoffs and shifts in production focus to plan timely recruitment.
2. Map Transferable Skills and Reassign Workforce
The current workforce, affected by temporary layoffs, holds skills that are valuable for new domestic production roles. Recruiters need to work with HR teams and line managers to identify which skills can be reassigned to support increased domestic capacity and new job functions.
Key steps include:
Skill Audit:
- Conduct a detailed review of job roles affected by the production shifts and extract the technical and soft skills that lay the foundation for other manufacturing roles.
- Assess the proficiency of technicians, engineers, and quality control experts who have experience from international facilities.
Reassignment Focus:
- Identify roles in domestic operations that require knowledge of advanced assembly methods and process adjustments due to higher production costs.
- Collaborate with operations managers to prepare lists of promising candidates for roles in quality control, production supervision, and supply chain coordination.
Training and Certification:
- Initiate targeted training programs that help workers adapt to local production processes.
- Work with technical schools and training centers to offer short-term certification courses in areas where domestic production is increasing.
3. Restructure Recruitment Campaigns and Team Roles
As the automotive manufacturers shift production back to U.S. facilities, companies are reworking their organizational structures. Recruiters should guide this restructuring process to reduce the gap between current talent supply and changing operational requirements. Actions include:
New Role Designation:
- Create job descriptions that reflect the new tasks emerging in domestic production settings. For instance, roles in regulatory compliance, technical oversight, and production process refinement are becoming increasingly necessary.
- Identify new positions that may not have existed before, such as roles connected to handling revised supply chain management under USMCA guidelines.
Internal Reassignment Programs:
- Develop programs that encourage laid-off workers to apply for open positions that match their transferable skills.
- Work with management to set up in-house career fairs or re-skilling sessions, giving employees a second chance to remain within the company in a different capacity.
External Hiring Initiatives:
- Launch recruitment drives targeted at specific skill sets that have been identified as necessary for increased domestic production, such as experienced production supervisors or advanced technicians who can adjust to new manufacturing protocols.
- Focus on sourcing candidates who have previously worked in settings that align with a more domestically centered production model.
Summary of Strategic Steps
- Track Trade to Talent: Regularly monitor production and policy updates; collect data to define new hiring needs.
- Map Transferable Skills: Conduct audits to identify re-assignable skills; set up training programs and certification courses tailored to domestic operations.
- Restructure Recruitment Initiatives: Redesign job roles in line with domestic production shifts; promote internal reassignments and initiate focused external recruitment campaigns
Conclusion: From Disruption to Design
The changes imposed in March and early April 2025 by U.S. tariff policies have forced a re-evaluation of production methods and hiring practices in the automotive sector. These actions are affecting supply chains and driving companies to bring production back to domestic facilities.
Recruiters play a critical role in guiding their organizations through these changes by reallocating skill sets. They must capture the surplus of experienced workers and help reassign them into new job roles that arise because of production changes. This approach has already yielded targeted hiring strategies in response to the short-term necessity for workforce realignment.
FAQs
1. What impact has the new 25% tariff had on automotive manufacturing operations?
The tariff forced companies like Stellantis to pause production overseas, resulting in layoffs of over 900 workers. This change has shifted production to U.S. plants, altered supply chain management, and affected investor sentiment. The production pause has also created a pool of skilled workers available for reassignment within domestic facilities.
2. How have major U.S. automakers reacted to these tariff changes?
Investor confidence has dropped as share prices for companies such as General Motors and Ford declined. The increased cost of production along with supply chain adjustments drove these market moves. Automakers are now reassessing cost structures and shifting operations toward domestic sites to better manage these pressures.
3. What opportunities does the surplus of skilled automotive workers present?
The availability of experienced technicians, engineers, and production specialists opens up new recruitment prospects. These professionals’ practical experience from international operations can be redirected to domestic roles. Recruiters can match this talent with emerging positions and support in-house training programs that fit the current production model.
4. How should recruiters adjust their strategies in response to these changes?
Recruiters need to closely track policy updates and production shifts. This involves performing skills audits, revising job descriptions, and encouraging internal reassignments. By aligning available talent with new roles emerging from domestic operations, they can help fill gaps resulting from the recent production adjustments.
5. What measures can companies take to support employees affected by production shifts?
Companies should plan targeted training and certification sessions to help affected workers transition into new roles. Initiatives like internal job fairs and skills assessments can match available talent with emerging job requirements. This approach offers a path for workers to maintain their employment within the company while meeting updated production needs.